First, the preface
This article refers to the address: http://
Computer Internet, wireless communication, and satellite navigation are called the three pillar industries of the information society. According to analysis, by 2030, it has been a period of rapid development of satellite navigation products. With the continuous advancement of technology, satellite navigation products are used in all aspects of people's lives: mapping, logistics, surveillance, security, handheld / car navigation, mobile phones and so on. The satellite navigation products that consumers can choose from in the market are also diverse and colorful.
However, the common problem facing consumers and manufacturers is: how to ensure that my satellite navigation products are excellent in function? For consumers, as long as they purchase satellite navigation products, they will have strong dependence on them. Therefore, after quality problems occur, most people will make quality complaints in the first time. For the manufacturer, the product inspection before leaving the factory is the lifeline to ensure the quality of the product, and it also avoids the large-scale complaints from consumers after the product leaves the factory.
This paper introduces the satellite navigation product testing system based on the NS600 12-channel GPS simulator independently developed and produced by Dongfang Lianxing. I hope that after reading this article, it will help you in the testing process of your product.
Second, the test plan
2.1 Problems that are easy to produce during the production process
• Selection of source materials: There are many source devices in satellite navigation products, such as GPS modules, GPS antennas, etc. Therefore, the quality of the source material directly determines the pros and cons of the final product.
• Choice of test plan: There are many factories that don't have a good test solution. Some of the existing ones also use a repeater or a single-channel simulator as a test source for the signal source. This has certain drawbacks. The indicators tested are not very reliable.
The repeater solution can solve the signal coverage problem in the factory, but because the satellite intensity in the sky is unknown, and each
Different satellite signals can only be used for qualitative analysis and cannot be used as a basis for quantitative measurement.
The single channel solution can solve the sensitivity problem of testing a single channel, but because there is only one channel number, it cannot be started.
Measurement of indicators such as time and positioning accuracy.
• Choice of test method: Test the quality of a satellite navigation product, and perform board level test and complete machine test, so as to ensure the quality of the product in all aspects.
• Incomplete test indicators: When testing, generally perform sensitivity test and cold start positioning time test. More requirements may also mention positioning accuracy testing, dynamic consistency testing, and more.
2.2 Production test flow chart
According to our experience, the production and testing process of satellite navigation products is shown in the following figure:
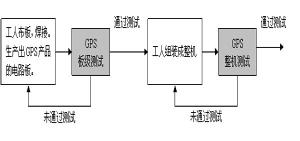
2.3 GPS board level test
Here is mainly a series of tests on the produced circuit board, the parameters of the test are: receiving sensitivity, cold start time, hot start time, positioning accuracy and so on. Board-level testing is very important in the manufacturing process. It can check the quality of the product at the beginning of production, completely eliminating the impact of problems such as worker welding or raw material damage on product performance.
The wired connection is usually used in the board level test, that is, the GPS signal is wired directly to the antenna interface on the circuit board at each test station. The advantage of this is that the board is fully tested without any external interference.
The main indicators tested here are: receiving sensitivity, cold start time, hot start time, positioning accuracy, and so on. The test method is that the manufacturer selects a Gold Sample and tests it based on this standard.
The figure below shows the difference in receiving sensitivity between the board under test and the gold standard. It can be clearly seen that the GPS receiver on the right is significantly inferior to the standard GPS receiver on the left in terms of the number of receiving channels and the sensitivity index. In this way, it can be considered that the circuit board on the right needs to be inspected and cannot enter the subsequent production.
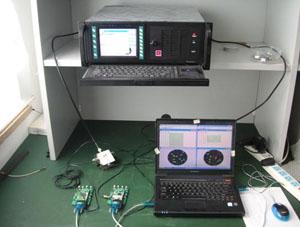
Board level test station schematic
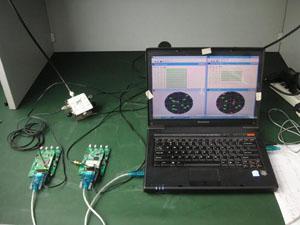
Sensitivity difference map
Because the NS600 12-channel GPS signal source can simultaneously transmit 12 GPS satellite signals of the same power intensity, the test here is a standard quantitative analysis, and the result is very reliable. At the same time, compared to the single-channel simulator, the NS600 can also be used to test GPS receiver start-up time, positioning accuracy and other indicators, completely ensuring board-level consistency.
2.4 GPS test
Through the board of the board level test, the subsequent production line is assembled into a complete machine. Before leaving the factory, test the whole machine in a wireless environment. The indicators tested here are: receiver sensitivity, start-up time, etc. The schematic diagram of the station is as follows:
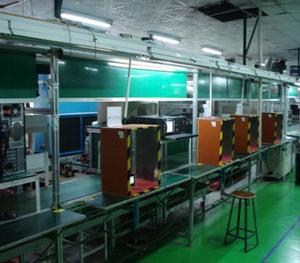
One-fourth station with shielded box
As shown in the above figure, the worker placed the tested product in a fixed position inside the shielding box and tested according to the factory specifications. Generally, it takes no more than 2 minutes to test a finished product, which improves the quality of the product while ensuring the output. For example, a one-four-station, 24 hours can guarantee a test volume of 2,880 units.
Third, the overall test platform to build
The schematic diagram of the connection of building a one-eighth station is as follows. This system includes four board-level test stations and four whole-machine test stations.
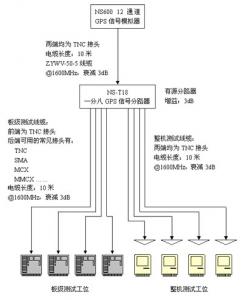
Instrument configuration
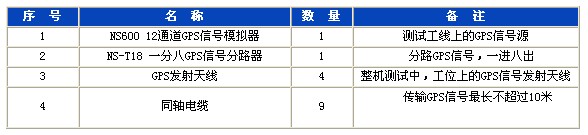
We provide Wire Harness manufacturing services for cable harnesses and built-to-print cables used in many industries, such as computer, game machine, POS machine, ATM , audio/video, electro-mechanical, data communications, telecommunications, medical, etc.
Related Products:Speaker Cable,Customized Cable Assemblies,electrical cable assemblies.
We have developed a tradition of high-tech engineering, prototyping, and quality Custom Cable manufacturing at very competitive pricing. Also with professional flow chart (wire cutting-stripping-copper twisting-crimping-crimping 100% inspection-soldering-molding-asssembling-testing-FQC100% -OQC) , which can help us support customers with stable quality.
Speaker Cable,Straight Bnc Cable Assembly,Idc Red Custom Cable Assembly,Customized Cable Assemblies,EV Cable Assemblies,Cable Assembly,Custom Cable,Customized Cable Assemblies
ETOP WIREHARNESS LIMITED , https://www.etopwireharness.com