I. Introduction
This article refers to the address: http://
Industrial fieldbus technology is one of the most concerned technologies in the automation industry in recent years, bringing great progress to automation control technology. The traditional field-level control system is not open, can be poorly integrated, and reliability is not guaranteed. Fieldbus Control System (FCS) uses a communication cable to connect field devices (intelligent, with communication interface), replaces 4-20mA/24VDC signals with digital communication, and completes field device control, monitoring, and remote parameterization. And other functions. It has many advantages, and has obvious advantages in the field of industrial automation, such as high integration, simple configuration, convenient design and installation, easy maintenance and expansion, saving hardware and software investment, etc., enabling advanced field device management functions to be realized. Fieldbus has been widely used in various fields, such as power monitoring and energy management.
The WISCO Iron Works began to use the fieldbus from the new construction of the No. 6 blast furnace in 2003, which is the first in the country to use the bus in the blast furnace system. At the beginning of the No. 6 blast furnace, an accident led to a fire in the main control building, and almost all electrical circuits of the furnace top fabric and the hot blast stove system were burned out. At least half a month of recovery time according to the traditional site-level control method, but Because of the use of the field bus, the number of cables is very small, we only resumed production in three days, so that the blast furnace resumed production ten days in advance, highlighting the blast furnace fieldbus control system in terms of maintenance and repair compared to the traditional site. The powerful advantage of the control method. The application of fieldbus technology in the iron and steel plant of Wuhan Iron and Steel Co., Ltd. has greatly improved the control and stability of the electrical equipment of the blast furnace. It has been promoted in other blast furnaces and achieved good results in the ironworks.
The status quo and deficiency of the traditional blast furnace automation control system
The blast furnace system is mainly composed of the top loading system, the tank upper and lower tank feeding system, the hoisting system, the coal injection system, the hot blast stove system, the pre-furnace tapping field system and the INBA slag treatment system. The production process is complicated and scattered. Many points, special environmental conditions, and very high requirements for electrical equipment, which results in a very complex electrical automation system, high failure rate and large maintenance.
At present, the control adopted by China's blast furnace is basically a traditional on-site control method. Traditional field-level and workshop-level automation monitoring and information integration systems (including: distributed control systems based on PC, PLC, DCS products), one of the main features is that the connection between the field layer device and the controller is a pair One (one I/O point to device measurement and control point) so-called I / O wiring, signal transmission 4-20mA (transmit analog information) or 24VDC (transfer switch information) signal. As shown in Figure 1:
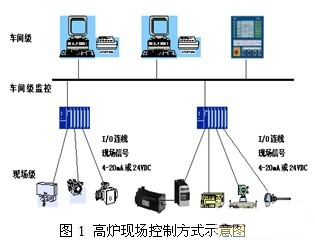
As can be seen from the figure, this traditional field-level automated monitoring system has several disadvantages:
(1) The information integration capability is not strong;
(2) The system is not open, the integration is poor, and the professionalism is not strong;
(3) Reliability is not easy to guarantee, and its main disadvantage is the bottleneck at the entrance of the host.
Due to the large number of on-site and equipment, and scattered, after the signal enters the PLC, it must undergo the conversion process of A/D and D/A, and the accuracy is reduced, forcing the scanning cycle of PLC to lengthen, which makes the performance of the whole host decline, threatening Real-time performance of various signals in the blast furnace. Affects the stability and reliability of the blast furnace control system.
The principle and characteristics of the blast furnace automation control system based on fieldbus
Profibus is the only fully integrated H1 (process) and H2 (factory automation) fieldbus solution and is an open fieldbus standard that is independent of the manufacturer. With the Profibus standard system, the equipment parts produced by different manufacturers must be specially adapted to communicate with their interfaces. Profibus can be used for high-speed and time-critical data transmission, as well as for a wide range of complex communication applications.
According to the application characteristics, Profibus is divided into three compatible versions: Profibus-DP, Profibus-FMS and Profibus-PA. Among them, Profibus-DP (H2) is an optimized high-speed communication connection designed for communication between automatic control system and device-level distributed I/O. It can be used for high-speed data transmission of distributed control systems. The rate can reach 12Mbit/s, which generally constitutes a single master system.
Profibus is characterized by the ability to network a decentralized digital controller from the field level to the shop floor, which is divided into a master station and a slave station. The primary station determines the data communication of the bus. When the primary station obtains the bus control right (token), it can actively send information without external requests. Slave is a peripheral device. Typical slaves include input and output devices, controllers, drivers, and measurement transmitters. They do not have bus control, only acknowledge the received message or send a message to the slave when the master makes a request.
Fieldbus is a network system and control system that uses a single distributed, digital, intelligent measurement and control device as a network node, connected by bus, realizes mutual exchange of information, and jointly completes automatic control functions. It is suitable for replacing the expensive 24V DC and 4-20mA measurement signal parallel transmission lines. While saving lines and equipment, it also provides field-level control functions for the Ethernet system of the WISCO Iron Works. The principle is as shown in Figure 2:
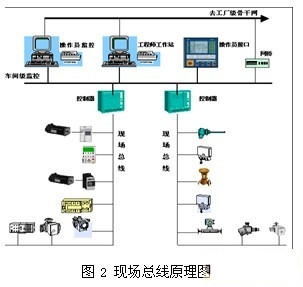
From the figure we can see that the fieldbus has the following main advantages:
(1) Reduce equipment (such as isolators, terminal points) and save engineering costs.
(2) Since the D/A and A/D conversion process is eliminated, the signal accuracy r is improved.
(3) It can avoid the signal jam caused by the detection signals of thousands of detection points and control points being collected at the entrance of DCS, but the control function is put down to the site, which increases the reliability of the system.
(4) Simple configuration, easy installation, operation and maintenance;
(5) The IP67 protection grade is made to be completely suitable for the harsh environment of the blast furnace site.
Bus monitoring and configuration method of Siwu Steel Ironmaking Plant
4.1 bus interface with PLC
WISCO Ironmaking Plant adopts Schneider PLC (Quantum series), which uses PTQ module to configure the bus. PTQ module supports industrial bus Profibus-DP protocol. It has strong expandability. A PTQ module is attached to the rack, and Profibus is used. The -DP protocol collects data from the industrial bus and controls the operation of field devices. Through the GSD file provided by Turck, the ProSoft Configuration Builder bus configuration software is used to complete the configuration of the bus, and then the Schneider PLC programming software Concept is used to import the configured files, and then the monitoring and operation of the bus device is completed through the program. The configuration diagram is shown in Figure 3:

4.2 Computer Monitoring
In the bus monitoring screen, we use Wonderware's Intouch software to monitor and monitor the communication status of each bus module. When a bus alarm occurs, we can quickly confirm the faulty device through the bus, effectively improving the fault. The time for repairs.
Five application effects and future prospects
The use of field bus avoids a large number of point-to-point cable laying, which reduces the difficulty of circuit laying design and the complexity of construction, saves the cost of investment, installation, commissioning and maintenance, and is convenient for maintenance, reducing the number of blast furnace breaks. The production of the ironworks brought direct economic benefits and received good results.
In the face of the challenges of the industrial technology revolution, we should seize the opportunity. The application of fieldbus technology in the automation control system will surely have more and more fields and spaces, which will promote our development.
UV Curing Screen Protector is an innovative product category. It is a Screen protector made by UV curing technology. This Screen protector has many unique features and advantages, which can provide excellent protection and use experience for various types of electronic devices.
Firstly, the UV Curing Screen Protector is made using advanced UV curing technology. This technology can form a hard and wear-resistant protective layer on the surface of the protective film, effectively resisting scratches, fingerprints, and other common screen damage.
Compared to traditional plastic protective films, UV Curing Screen Protector has higher hardness and durability, which can better protect device screens.
Secondly, the UV Curing Screen Protector has excellent transparency and tactile feel. Due to the use of high-quality materials and advanced production technology, this Screen protector can provide a clear and transparent screen display effect without affecting the viewing experience of the device. In addition, it also has a good tactile feel and can provide smooth touch operation, making users feel more comfortable and natural when using the device.
In addition, the UV Curing Screen Protector also has anti glare and anti blue light functions. With the popularization of electronic devices and the increase in usage time, people's attention to screen radiation and glare is also increasing. UV Curing Screen Protector uses special optical coating technology to effectively reduce screen reflections and glare, protecting users' eyes from harm. In addition, it can also filter out harmful blue light, reduce damage to the eyes, and provide a more comfortable and healthy user experience.
Finally, the UV Curing Screen Protector has the characteristics of simplicity and ease of use. It adopts a self-adhesive design, which simply applies the protective film to the device screen without the need for additional glue or pasting tools. At the same time, it also has the characteristic of being easy to clean, simply wipe with a clean cloth to remove stains and fingerprints, and keep the screen clean and smooth.
Uv Curing Screen Protector,Uv Curing Film Sheets,UV Cured Screen Protector,UV Screen Protector,UV Light Screen Protector
Guangdong Magic Electronic Limited , https://www.magicmax.cc