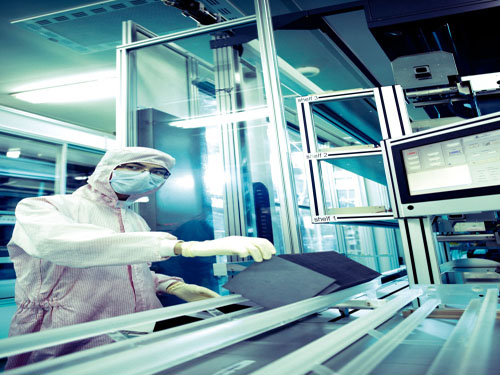
Slower growth in foreign demand, domestic polysilicon squeeze faced by imported products: yet to upgrade the core competitiveness through technology director of China Electronics Materials Industry Association, Industrial Technology Innovation Alliance polysilicon Secretary-General Lu Jin <br> <br> development of domestic polysilicon industry The important mission that the industry shoulders. China's semiconductor industry, photovoltaic industry development and even the development of the defense industry can not be separated from China's own polysilicon industry. Solar photovoltaic industry is an important part of strategic emerging industries, and it is also an important guarantee for the transformation of China's energy structure, responding to climate change, and fulfilling emission reduction targets. As the basic raw material for solar photovoltaic power generation, polysilicon has important strategic significance for the healthy development of its industry. The United States, Japan and other developed countries all regard it as an important strategic material. It is the rapid development and growth of China's polysilicon industry that only supported China's solar cell output ranks first in the world for five consecutive years. Nowadays, the slowdown in demand growth in foreign markets, the intensification of domestic and foreign market competition, and the deep-seated internal contradictions in the industry have once again made China's polysilicon industry stand at the forefront of opportunities and challenges. China's polysilicon industry urgently needs to improve its industrial structure, promote industrial support, and increase its core competitiveness in scale and cost.
Production has accounted for 35% of the world
China's polysilicon production accounts for about 35% of the world's total. By the end of 2012, China's polysilicon production capacity will reach 200,000 tons.
In 2011, on the one hand, due to the European debt crisis, the major markets of photovoltaic products—European countries have significantly reduced policy subsidies, which has greatly impacted the PV industry; on the other hand, during the first half of 2010–2011, The investment in the photovoltaic industry has been continuously increased, and the production capacity has been greatly expanded, making the global solar cell product inventory pressure prominent. The photovoltaic industry entered a new round of adjustment period, and the domestic polysilicon industry was also deeply affected by this.
In 2011, with the release of polysilicon companies' new and expanded production capacity, global polysilicon production continued to grow. In 2011, the total global output reached 240,000 tons, an increase of 30% year-on-year in 2010. It is expected that there will still be around 30% growth in 2012. Globally, the supply and demand of the polysilicon market is basically balanced or slightly higher than demand. Driven by the development of the photovoltaic industry, China's domestic demand for polysilicon also increases year by year. From 16,544 tons of consumption in 2008 to 146,131 tons in 2011.
According to the latest survey by China Electronic Materials Industry Association, the domestic polysilicon production in 2011 reached 82,768 tons, an increase of 84% from 450,021 tons in 2010. The industry still maintains a momentum of rapid growth. From 2006 to 2011, China's polysilicon production has doubled, with an average annual increase of more than 100%. In 2011, the annual sales exceeded 23 billion yuan, which was basically the same as in 2010; the total number of employed people exceeded 15,000, of which more than 5,000 were technical personnel. By the end of 2011, the total capacity of China's polysilicon production line has reached 148,000 tons. It is expected that by the end of 2012, China's polysilicon production capacity will reach 200,000 tons. China's polysilicon production accounts for about 35% of the world's total, and has become the world's largest producer of polysilicon after the United States and Germany.
In recent years, domestic polysilicon production enterprises have achieved rapid development and have broken the international polysilicon production pattern. Some of China's enterprises, such as Jiangsu Zhongneng, LDK Solar, Luoyang Zhongsi, and Chongqing Daquan, are among the top companies in the world. Jiangsu Zhongneng became the third largest polysilicon producer in the world with annual production of nearly 30,000 tons and capacity of 46,000 tons. Its polysilicon production accounted for 36% of the total domestic production. LDK annual output has also exceeded 10,000 tons.
The large-scale production system has been formed in the production practice, and has broken through and mastered the key technologies for the scaled production of the modified Siemens method.
China's polysilicon industrialization technology has been continuously improved. In recent years, China's polysilicon industry has doubled its annual production capacity, and the company has accumulated through production practices through independent research and development, the introduction of foreign advanced technologies, and digestion and absorption. It has broken through and mastered the scaled production of the modified Siemens method. Key technologies, large-scale polysilicon production system has been formed.
The Ministry of Industry and Information Technology of the “12th Five-Year Development Plan for Solar Photovoltaic Industry†reports that during the “11th Five-Year Plan†period, China’s photovoltaic industry achieved remarkable results in energy conservation and emission reduction, and the comprehensive utilization of by-product water steadily improved, and overall resource utilization rate increased. Significant improvement. According to the latest statistics from the China Electronic Materials Industry Association, the average integrated power consumption of domestic polysilicon enterprises has been reduced from 300 to 150 kwh per kilogram of polysilicon produced in 2006, which was reduced from 80 to 150 kwh per year. Some advanced technology companies even It has been less than 80 kWh. The direct production cost of polysilicon is also reduced from the original 70 US dollars/kg to the current 25~40 US dollars/kg, and the production cost of a few polysilicon enterprises has dropped to 20 US dollars/kg, reaching the international advanced level. And most companies are still optimizing the process in order to further reduce production energy consumption and costs. The plan gives full recognition to the development of China's polysilicon industry during the “Eleventh Five-Year Plan†period. It will list high-purity polysilicon as the “Twelfth Five-Year Plan†development focus, and pointed out that “supporting backbone enterprises will be better and stronger, and by 2015, polysilicon Leading companies have reached 50,000 tons, backbone enterprises have reached 10,000 tons, and "polysilicon production has achieved simultaneous increase in industrial scale, product quality and environmental protection level. By 2015, the average integrated power consumption is less than 120 kWh/kg."
The pollution problem has been effectively solved The environmental problem of polysilicon has no technical bottleneck. The “source of pollution†is simple, easy to handle, and easy to prevent and control.
Polysilicon production itself has higher unit power consumption, but at the same time it also has the characteristics of high-tech content, high added value, and high production value, and its energy consumption structure is relatively single (mainly for electricity), and its comprehensive energy consumption per unit of production value is comparable to other industries. The ratio is not too high. At present, the mainstream energy consumption of the industry reaches 80-150 kWh/kg of polysilicon, the energy consumption per unit of industrial added value for polysilicon production is between 0.6 and 1 ton of standard coal, and the national average energy consumption per unit of industrial added value (1.92 ton of standard coal / 10,000 yuan, compared with 2010 is not high, is a typical energy-efficient products. The energy-saving and consumption-reduction technologies have received the unanimous attention of domestic enterprises and are the key to reducing production costs. At present, related technologies are still being researched and developed, which is expected to further reduce energy consumption. The energy consumption per million yuan of industrial output value of the entire photovoltaic industry chain is even lower.
In addition, from the "energy recovery ratio" concept, from the production of industrial silicon to the production of solar modules, the current level of technology, a total of less than 250 kwh per kilogram of silicon power consumption (including polysilicon production, single crystal pulling / ingot casting , slicing, battery cell manufacturing, component packaging and other links), and polycrystalline silicon raw materials per kilowatt of solar cells need 7 kilograms. According to the conservative calculation of the distribution of solar energy resources in our country, the solar cell per watt can generate about 1.5 kWh per year, and the service life of the solar cell is 20 years. The energy regeneration ratio of the silicon solar cell can be calculated as: 1.5×20×1000/(250 ×7) ≈ 17. That is, all the electric energy consumed in the whole process of manufacturing a silicon solar cell (from industrial silicon to a Battery Pack ) can be recovered within about 2 years of use. Therefore, the polysilicon industry is not a high-energy-consuming industry.
The environmental protection issue of polysilicon production is also a major concern for domestic polysilicon companies and all walks of life. Improved Siemens polysilicon production in the process (such as chlorosilane synthesis, reduction, hydrogenation, etc.) will be accompanied by a large amount of hydrogen, hydrogen chloride, trichlorosilane and silicon tetrachloride, among which the main by-product is silicon tetrachloride. , hydrogen chloride, hydrogen, and high and low boiling materials. It should be said that from a technical point of view, there is no technical bottleneck in the environmental protection issue of polysilicon. Compared to other chemical companies, the "pollution source" of polysilicon is simple, easy to handle, and easy to prevent and control. Judging from the status of China's polysilicon industry, the utilization of polysilicon production by-products has become an important part of the production of polysilicon. There are many kinds of by-product silicon tetrachloride treatment methods, and the effect of its outlet or comprehensive utilization is directly related to the economic benefits, energy consumption and environmental protection of polysilicon production, and even relates to the normal operation of polysilicon production lines.
For the recycling of silicon tetrachloride, the current layout of domestic enterprises is more suitable for the use of hydrogenation treatment, which will be converted into trichlorosilane reuse, which not only solves the emission problem, but also increase the output of polysilicon. At present, most of the polysilicon enterprises that have already put into operation in China have already solved the problem of all-material recycling and clean production; some are undergoing treatment through export, comprehensive utilization, and pollution-free treatment in the process of technological transformation and upgrading, and no longer have any emissions. phenomenon. Polysilicon production in the production of high and low boiling materials and other difficult to recover by-products, the majority of domestic companies currently adopt the rinse, alkali and other methods of treatment, some companies have also invested disproportionate treatment, white carbon preparation and other equipment for processing. To effectively and reasonably handle the by-products of polysilicon is not only the requirement for emission reduction and environmental protection, but also conducive to improving the overall economic benefits of the enterprise. Therefore, the problem of pollution caused by polysilicon production has also been solved.
Low-priced imported products hit the domestic market The giant polysilicon manufacturers such as Korea and the US continue to increase the dumping of low-priced products to the Chinese market.
In 2011, the global PV market experienced ups and downs, and the market price of polysilicon products had also been declining from the 80 US dollars/kg at the beginning of the year to the current US$30/kg, a drop of 60%. This is certainly due to the fact that domestic polysilicon companies have improved their technological level, reduced costs, released production capacity, and reduced downstream demand. The more important reason is that the polysilicon product market is a globalized market. Foreign companies use its large scale, low cost, and low prices. The advantage of attracting domestic downstream manufacturers and circumventing risks by binding long-term contracts and high liquidated damages to downstream companies. At present, most of the polysilicon enterprises in China have a large gap with the world's largest companies in terms of their technological level, industry scale, and innovation capability, as well as their financial support and government support and support, and their competitiveness is obviously weak.
As far as the domestic market is concerned, the actual output of domestic polysilicon is still far less than the demand, but a large number of imported products surged to squeeze the domestic market. In particular, the giant polysilicon manufacturers such as Korea and the United States continuously increased the dumping of low-priced products to the Chinese market. According to customs statistics, China imported 64,600 tons of polysilicon in 2011, an increase of 36% year-on-year; import volume was 3.8 billion US dollars, up 42% year-on-year. In particular, South Korea surpassed the United States in April 2011 to become China's largest polysilicon importer, and exports accounted for 32.2% of China's total polysilicon imports. In order to compete for the Chinese market, OCI's long unit price is cheaper than the domestic average price of 30,000 to 80,000 yuan / ton, the spot price of 50,000 to 100,000 yuan / ton cheaper, particularly impact on China's polysilicon market.
There are nearly forty polysilicon production enterprises in China, and most companies have an annual production capacity of 1,000 to 3,000 tons, and even have an annual production scale of less than 1,000 tons. Some companies have not put in production for a long time, and the technology needs to be further improved. The investment cost of the production line that was built before 2009 is high, and the energy consumption of the equipment is high. As a result, the cost of the integrated product of the enterprise is relatively high. At present, the polysilicon market price is 30 US dollars/kg, which is already lower than the production cost of many domestic polysilicon enterprises. In the process of product price decline, large enterprises have strong survivability, and the market has instead concentrated on leading companies. A large number of polysilicon enterprises in China have been forced to suspend production and production cuts. In particular, since the fourth quarter of last year, the capacity utilization rate of domestic enterprises has declined rapidly, and the inventory has soared. Many companies have faced greater threats to survival.
Military battery has a wide application on some high-tech euquipment including military communications equipment, submarine, drone , warship, government and so on .
The design for Military Battery Pack is more strict than normal lithium or Lipo Battery packs ,because it must meet some tough requirements as ;
1, high-level safety : military Lithium Battery was demanded to provide high-level safety and will not cause any death or accident with High intensity impact and and hit.
2, high reliability: the Military Battery must be reliable and could not causing any problems to the equipments during operating .
3, High environmental adaptability: the military battery pack is demanded to use in different temperature ,air pressure and other enviornmental condition.
Military Batteries : Ni-Mh Battery Pack BB-390/U
Besides ,the military always have a strict standard on low power self-consuming and deep life cycles .so these above standard has made it special from the other Lithium Battery Pack or other battery packs which applied to life .
Military Batteries
Military Batteries,Military Battery,Military Vehicle Battery,Military Solar Battery
YFJ TECHNOLOGY (HK) CO.,LIMITED , http://www.yfjpower.com